Metal buildings are a popular choice in West Virginia and for good reason. They offer durability, versatility, and cost-effectiveness for any type of building. From storage sheds to commercial structures, these buildings can withstand the state’s diverse weather conditions.
COMPARE PRICES & SAVE UP TO 33%
Metal buildings in West Virginia provide excellent protection against severe weather, including heavy snow, high winds, and storms. Their strength comes from high-quality steel construction, engineered to meet local building codes and stand up to the elements. This makes them a smart investment for property owners looking for long-lasting structures.
West Virginia metal buildings can be customized for many uses. They work well as garages, barns, warehouses, and even industrial facilities. With options for insulation, windows, doors, and various finishes, these buildings can be tailored to fit specific needs and blend in with their surroundings.
What are the average costs for a metal building in West Virginia per square foot?
In West Virginia, the cost of metal buildings varies based on several factors. Metal building prices typically range from $15 to $25 per square foot for basic prefab kits.
For a complete installed structure, costs will increase. Turnkey metal buildings in West Virginia usually run between $25 and $48 per square foot. This price includes the kit, concrete foundation, delivery, and construction.
Factors affecting the final cost include:
- Overall building size
- Design complexity
- Local labor rates
- Material quality
It’s important to get quotes from multiple suppliers. Prices can vary significantly between companies. Requesting detailed estimates helps ensure accurate budgeting for West Virginia metal building projects.
4 Key Benefits of Metal Buildings In West Virginia
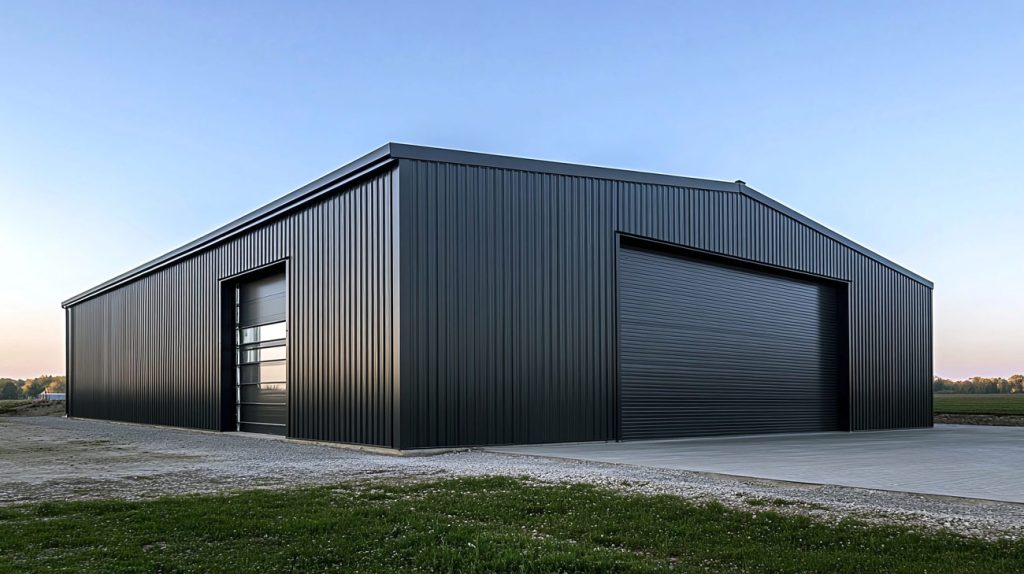
Metal buildings offer many advantages for West Virginia property owners. They stand up well to the state’s varied weather conditions and provide flexible, cost-effective solutions for many needs.
#1 – Durability and Longevity
Metal buildings in West Virginia are built to last. They resist damage from harsh weather, including heavy snow and strong winds. Steel structures don’t rot, warp, or attract pests like wood does.
This means less maintenance over time. Owners spend less on repairs and upkeep. The buildings keep their strength and looks for many years.
Metal roofs shed snow easily, reducing the risk of collapse. They also stand up to acid rain better than other materials. This is important in parts of West Virginia affected by industrial emissions.
#2 – Cost-Effectiveness
Metal buildings save money in several ways. They go up faster than traditional buildings, cutting labor costs. The materials often cost less too.
Insurance rates may be lower for metal buildings. They resist fire and weather damage better than wood structures. This makes them safer and less risky to insure.
Energy efficiency is another money-saver. Metal buildings can be well-insulated. This keeps heating and cooling costs down in West Virginia’s hot summers and cold winters.
Maintenance costs stay low over the years. Metal doesn’t need painting or treatments like wood does. It keeps its good looks with minimal care.
#3 – Sustainability
Steel used in metal buildings is often recycled. This reduces the demand for new raw materials. At the end of the building’s life, the steel can be recycled again.
Metal roofs reflect sunlight. This helps keep buildings cooler in summer, saving on air conditioning. Some metal roofs can be coated to boost this effect even more.
These buildings can be designed for good airflow. This cuts down on the need for artificial cooling. It also helps prevent moisture problems that can lead to mold.
Metal doesn’t give off harmful gases like some building materials do. This leads to better air quality inside the building.
#4 – Versatility
Metal buildings serve many purposes in West Virginia.
They work well for:
- Farms (barns, equipment storage)
- Businesses (warehouses, offices, shops)
- Homes (garages, barndominiums, workshops)
- Community buildings (churches, sports centers)
Large, open interiors are easy to create with clear span metal buildings. This makes them great for storage or manufacturing. But they can also be divided into smaller spaces for offices or apartments.
Metal buildings can be designed to match any style. They fit in well with West Virginia’s mix of rural and urban areas. Custom colors and finishes help them blend with their surroundings.
WV Climate Considerations
West Virginia’s varied climate affects metal building design. Key factors include weather resistance and energy efficiency measures to handle temperature swings.
Weather Resistance
West Virginia’s climate includes hot summers and cold winters. Metal buildings must withstand:
- Heavy snowfall in winter
- Thunderstorms and flooding in summer
- Strong winds year-round
Steel structures offer excellent durability against these elements. They resist water damage better than wood. Proper coatings protect against rust and corrosion.
Roof design is crucial. Sloped roofs shed snow and rain efficiently. Gutters and downspouts direct water away from the foundation.
Insulation and Energy Efficiency
Temperature swings make insulation vital in West Virginia metal buildings.
This makes good insulation critical for:
- Keeping interiors warm in winter
- Maintaining cool temperatures in summer
- Reducing energy costs year-round
We recommend all new builds in the Mountain state use spray foam insulation. It works well in metal structures and fills all gaps to create an airtight seal.
Reflective roof coatings help in summer. They bounce back sunlight and heat. This lowers cooling needs.
Proper ventilation is important too. It prevents moisture buildup and improves air quality.
West Virginia Building Code & Zoning Laws
West Virginia has specific building codes that apply to metal buildings and other steel structures. The West Virginia State Fire Commission is in charge of adopting and updating these codes.
The state uses several International Code Council (ICC) standards. These include:
- 2015 International Building Code (IBC)
- 2015 International Energy Conservation Code (IECC)
- 2017 ICC A117.1 Accessible and Usable Buildings and Facilities
Contractors working on metal buildings must have a license. This ensures they know the rules and can build safely. It’s wise to check with local authorities about specific requirements. Rules can vary between cities and counties in West Virginia. County commissions can adopt building codes for their specific areas. These codes set minimum standards for safety.
West Virginia Permits
As we mentioned above, West Virginia, requires permits for most construction projects, including metal buildings. These permits ensure structures meet safety standards and local regulations.
To get a building permit in West Virginia, you need to submit an application to your local building inspector or municipality. The application typically includes building plans and other project details.
Zoning laws in West Virginia classify land into different categories based on intended use. These land use codes help regulate development and maintain community standards.
Some common land use codes in West Virginia include:
- Residential
- Commercial
- Industrial
- Agricultural
Metal buildings often fall under industrial or commercial codes, depending on their purpose. It’s important to check local zoning regulations before starting construction.
The West Virginia Department of Health and Human Resources also regulates certain types of construction, particularly for health facilities. These projects may require additional approvals.
Local authorities may have specific rules for metal buildings, such as height restrictions, setback requirements, and design standards. Always consult with local officials to ensure compliance.
Remember that permits and zoning laws can vary by city and county in West Virginia. It’s best to contact your local planning department for the most up-to-date information on building regulations in your area.
Metal Construction Uses In West Virginia
Metal buildings in West Virginia serve many purposes. They help businesses grow and provide homes for families. Let’s look at some real examples.
Commercial Projects
A car dealership in Charleston used a metal building for its showroom. The large open space lets them display many vehicles. The building stands up to harsh weather and keeps the cars safe.
A farm supply store in Huntington chose a metal structure for its warehouse. The building is 10,000 square feet. It has high ceilings to store tall farm equipment. The metal walls keep out pests and moisture.
A machine shop in Morgantown picked a steel building for its workshop. The shop needed strong walls to mount heavy tools. The metal frame easily supports overhead cranes.
Residential Structures
A family in Wheeling built a metal home. They chose a design that looks like a traditional house. The metal frame saved them money on building costs. The walls have good insulation to keep heating bills low.
A couple near Parkersburg made a vacation cabin from a metal kit. The small building went up quickly. It has big windows to enjoy the mountain views. The metal roof sheds snow easily in winter.
A homeowner in Beckley added a metal garage to their property. The garage matches the style of their main house. It has room for two cars and a workshop area. The sturdy walls keep their tools and vehicles secure.
Frequently Asked Questions
We hope we have made clear how metal buildings in West Virginia offer versatile and cost-effective construction solutions. Here are some common questions from our customers.
What are the average costs for a metal building per square foot in West Virginia?
Metal building costs in West Virginia typically range from $15 to $25 per square foot. Prices vary based on size, design complexity, and materials used.
Local factors like terrain and climate can impact costs. Larger structures often have lower per-square-foot costs due to economies of scale.
How do metal building prices vary in different cities across West Virginia, such as Charleston or Morgantown?
Prices for metal buildings fluctuate between cities in West Virginia. Charleston and Morgantown may have higher costs due to increased demand and labor rates.
Rural areas generally see lower prices. Factors like local building codes and accessibility also influence costs across different West Virginia locations.
What factors influence the total cost of constructing a metal garage in areas like Beckley, WV?
Several elements affect metal garage costs in Beckley. Size and design complexity are major factors. Custom features like windows, doors, and insulation increase expenses.
Site preparation, foundation work, and local permit fees also impact the total cost. Labor rates in Beckley compared to other areas can affect pricing as well.
Can you provide an estimate for the cost of a 40×60 steel home in West Virginia?
A 40×60 steel home in West Virginia might cost between $34,000 and $72,000 for the basic structure. This estimate covers the metal building kit but excludes extras.
Additional costs include concrete foundation, interior finishing, plumbing, and electrical work. These can significantly increase the total project price.
What should be taken into consideration when purchasing a metal building for sale in West Virginia?
When buying a metal building in West Virginia, consider local climate conditions. The state experiences heavy snowfall and high winds in some areas.
Ensure the building meets local zoning laws and building codes. Think about future expansion needs and customize accordingly.
What are the benefits of choosing metal buildings over traditional construction methods in West Virginia?
Metal buildings offer durability against West Virginia’s varied weather conditions. They resist pests, fire, and mold better than wood structures.
Construction time is typically faster for metal buildings. They also provide flexible customization options and can be more cost-effective in the long run due to lower maintenance needs.