Understanding Warehouse Construction Costs
Warehouse construction costs can vary widely depending on a variety of factors, including the size of the warehouse, the materials used, and the location of the warehouse. When considering the cost to build a warehouse, it’s important to understand the different types of costs involved, including hard costs, soft costs, and financing costs.
Let’s clarify those different types of expenses that will impact your overall budget.
COMPARE PRICES & SAVE UP TO 33%
Hard Costs
Hard costs are the direct costs associated with building a warehouse. These costs include materials, labor, and equipment costs. The cost of materials can vary depending on the type of construction used. For example, steel construction is generally less expensive than concrete construction. The cost of labor and equipment will also vary depending on the location of the warehouse and the complexity of the project.
Soft Costs
Soft costs are indirect costs associated with building a warehouse. These costs include design fees, permits, and other administrative costs. Soft costs can add up quickly and should be taken into consideration when budgeting for a warehouse construction project.
Financing Costs
Financing costs are the costs associated with obtaining financing for a warehouse construction project. These costs can include interest payments, loan fees, and other costs associated with obtaining a loan. It’s important to carefully consider financing options when planning a warehouse construction project to ensure that the project is financially feasible.
Understanding warehouse construction costs is an important part of planning a warehouse construction project. By taking into consideration hard costs, soft costs, and financing costs, it’s possible to create a realistic budget for a warehouse project.
How To Set up A Warehouse Construction Project
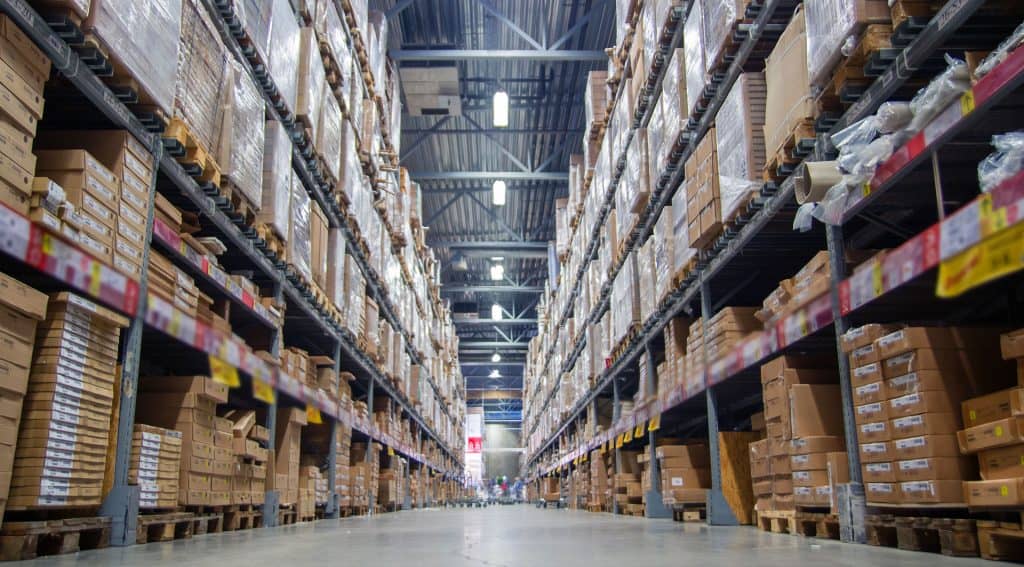
Step 1 – Determining the Size and Design of the Warehouse
When it comes to building a warehouse, one of the first decisions that needs to be made is the size and design of the building. The size of the warehouse will depend on the needs of the business, the amount of inventory that needs to be stored, and the number of employees that will be working in the warehouse.
The design of the warehouse will also depend on the needs of the business.
Some businesses may require a simple rectangular building, while others may need a more complex multistory warehouse. The building design will also depend on the type of inventory that will be stored in the warehouse. For example, if the warehouse will be used as a distribution center, it may require a different design than a warehouse that is used to store raw materials.
Metal construction is a popular choice for warehouse construction due to its durability and cost-effectiveness. When choosing a metal building, businesses should consider the following factors:
- The size of the warehouse: Metal buildings can be constructed in a wide range of sizes, from small storage sheds to large multistory warehouses. The size of the warehouse will depend on the needs of the business.
- The design of the warehouse: Metal buildings can be constructed in a variety of designs, from simple rectangular buildings to more complex designs with multiple levels and mezzanine floors.
- The type of inventory that will be stored in the warehouse: The design of the warehouse will also depend on the type of inventory that will be stored in the warehouse. For example, if the warehouse will be used to store heavy equipment, it may require a different design than a warehouse that is used to store small parts.
- The building codes and regulations in the area: Before constructing a metal warehouse, businesses should check the building codes and regulations in the area to ensure that the building meets all requirements.
Businesses should carefully consider the size and design of the warehouse before beginning construction. By choosing the right size and design, businesses can ensure that their warehouse meets their needs and is cost-effective.
Step 2 – Choosing the Warehouse Location
When it comes to building a warehouse, choosing the right location is crucial. The location of the warehouse can impact transportation costs, labor costs, and overall efficiency.
Here are some factors to consider when choosing a warehouse location:
Location
The location of the warehouse should be easily accessible from major highways and transportation hubs. This will minimize transportation costs and make it easier to move goods in and out of the warehouse. Additionally, the warehouse should be located in an area with a large labor pool. This will ensure that there are enough workers available to staff the warehouse.
Site
The site of the warehouse should be large enough to accommodate the warehouse and any necessary parking or loading areas. Additionally, the site should be zoned for industrial use and have the necessary permits and approvals for construction. It is also important to consider the environmental impact of the site and ensure that it is not located in a flood zone or other hazardous area.
Industrial Park Warehouse
Building a warehouse in an industrial park can offer many advantages. Industrial parks often have established infrastructure, such as roads, utilities, and transportation networks. Additionally, warehouses located in industrial parks may have access to shared services, such as security, maintenance, and landscaping.
To reiterate, choosing the right location for a warehouse is crucial for its success. By considering factors such as location, site, and construction materials, businesses can ensure that their warehouse is efficient, cost-effective, and environmentally friendly.
Common Materials Used in Warehouse Construction
When it comes to constructing a warehouse, the materials used can significantly impact the cost and durability of the building. Metal construction, including steel and metal cladding, is often used due to its affordability and durability. Obviously, we are biased to the use of metal and steel, but it goes well beyond our preference when you consider the size and load requirements for warehouses.
Steel frames can cost around $10-$20 per square foot, making them an affordable choice for many. In addition, steel is known for its strength and durability, making it an ideal material for a warehouse that needs to withstand heavy loads and harsh weather conditions.
Insulated concrete, also known as insulated concrete forms (ICF), is another popular material used in warehouse construction. ICFs are made of foam panels that are filled with concrete, providing excellent insulation and soundproofing. While ICFs can be more expensive than other materials, their energy efficiency and durability can save money in the long run.
Stud frames, made of wood or metal, are another option for warehouse construction. Wood stud frames can cost around $20-$40 per square foot. Wood stud frames may not be as durable as other materials and may require more maintenance over time. When you consider that fact, coupled with the similar price point to metal structures, it doesn’t make financial sense to choose wood materials for your warehouse.
When it comes to flooring, a concrete slab is a common choice for warehouse construction. Concrete slabs are durable and can withstand heavy loads, making them ideal for a warehouse setting. However, the cost of a concrete slab can vary depending on the size of the warehouse and the thickness of the slab.
The choice of materials for warehouse construction will depend on factors such as budget, durability, and energy efficiency. While metal construction is often the most affordable and durable option, other materials such as insulated concrete and stud frames may be more suitable for certain situations.
Other Warehouse Construction Costs To Consider
When it comes to building a warehouse, labor and equipment costs can make up a significant portion of the overall project cost. The cost of labor and equipment can vary depending on the location and the type of construction equipment used.
Labor Costs
Labor costs for building a warehouse can vary depending on the type and size of the project. Generally, the cost of labor for a metal warehouse construction project can range from $50 to $100 per hour. The cost of labor can also vary depending on the location of the project. For example, labor costs in urban areas tend to be higher than in rural areas.
Equipment Costs
Equipment costs for building a warehouse can also vary depending on the type of construction equipment used. For metal warehouse construction, some of the common types of equipment used include cranes, forklifts, and aerial lifts. The cost of equipment can range from $50,000 to $200,000 or more depending on the type and size of the equipment.
Construction Equipment
Construction equipment is a crucial part of building a warehouse. The cost of construction equipment can vary depending on the type and size of the equipment. For example, the cost of a forklift can range from $10,000 to $50,000, while the cost of a crane can range from $100,000 to $500,000 or more.
Machinery
Machinery costs can also be a significant part of the overall cost of building a warehouse. For example, the cost of a metal cutting machine can range from $10,000 to $100,000 or more depending on the size and type of machine. The cost of machinery can also vary depending on the location of the project.
Environmental Control
Environmental control is crucial for ensuring that the warehouse is a safe and comfortable environment for employees to work in. This includes regulating temperature, humidity, and air quality. The cost of environmental control will depend on the size of the warehouse, the climate in the region, and the type of equipment used. For example, a warehouse in a hot and humid climate will require more powerful air conditioning systems than one in a cooler climate.
Prefabricated vs Custom Warehouse
When it comes to building a warehouse, there are two main options available: prefabricated or custom. While both options have their own set of advantages and disadvantages, the cost is often the deciding factor for most businesses.
Prefabricated Warehouse Cost
Prefabricated or pre-engineered buildings are constructed off-site and then transported to the final location to be assembled. These buildings are often made of steel and are designed to be easily assembled and disassembled, making them a popular choice for businesses that need a temporary or movable warehouse.
The cost of a prefabricated warehouse depends on several factors, including the size of the building, the materials used, and the complexity of the design. On average, the cost of a prefabricated warehouse ranges between $7.50 to $40.00 per square foot, according to Fox Blocks.
Prefabricated warehouses are often cheaper than custom warehouses because they are designed to be mass-produced, which reduces the cost of labor and materials. Additionally, prefabricated warehouses can be assembled quickly, which reduces the cost of construction and minimizes downtime for businesses.
Custom Warehouse Kit Cost
Custom warehouses, on the other hand, are designed and built from scratch to meet the specific needs of the business. These warehouses can be made of a variety of materials, including steel, concrete, and wood, and can be designed to include specific features, such as loading docks, mezzanine levels, and specialized storage areas.
The cost of a custom warehouse depends on several factors, including the size of the building, the materials used, and the complexity of the design. According to The Korte Company, the cost of a custom warehouse can range from $20 to $100 per square foot, depending on the level of customization and the materials used.
Custom warehouses are often more expensive than prefabricated warehouses because they require more time and labor to design and construct. Additionally, custom warehouses may require special permits and inspections, which can increase the cost of construction.
Which Option is Right for Your Business?
When deciding between a prefabricated or custom warehouse, businesses should consider their specific needs and budget. Prefabricated warehouses are a good option for businesses that need a temporary or movable warehouse, or for those that need a warehouse quickly and at a lower cost. Custom warehouses are a good option for businesses that require specific features or have unique storage needs, but they come at a higher cost and longer construction time.
Frequently Asked Questions
What is the average cost per square foot to build an industrial warehouse?
The cost to build an industrial warehouse can vary based on different factors such as location, materials used, and complexity of the structure. According to Fox Blocks, the basic cost to build a steel warehouse ranges between $7.50 to $40.00 per square foot, while our company estimates the average turnkey cost to build a warehouse ranges from $19 to $60 per square foot.
How much does it cost to build a 100,000 square foot warehouse?
The cost to build a 100,000 square foot warehouse can vary based on the factors mentioned above. A ballpark estimate to build a 100,000-square-foot warehouse would be around $2.2 million to $4 million.
What is the construction cost calculator for warehouse building?
There are several online construction cost calculators available for pricing a warehouse structure. MetalBuildings.org provides free quotes for your warehouse building.
Our estimates include the cost to build a warehouse based on the square footage, location, and type of construction. RSMeans also offers a construction cost estimator tool that can be used to calculate the cost of building a warehouse.
How much does it cost to build a small warehouse?
The cost to build a small warehouse can vary based on the size and complexity of the structure. According to Strong Building Systems, a steel building will usually run between $7-$12 per square foot. Therefore, the estimated cost to build a small warehouse of 5,000 square feet would be around $35,000 to $60,000.
How long does it take to construct a warehouse?
The time it takes to construct a warehouse can vary based on the size and complexity of the structure. According to APX Construction Group, a warehouse can take anywhere from 6 to 12 months to construct, depending on the construction method and the size of the building.
What is the cost to build a 30,000 square foot warehouse?
The cost to build a 30,000-square-foot warehouse can vary based on the factors mentioned above. According to Crexi, warehouse construction prices range from $72 to $202.50 per square foot in select cities. Therefore, the estimated cost to build a 30,000 square foot warehouse would be around $2.05 million to $6 million.